Melamine Faced Chipboard (MFC) for high quality fitted furniture
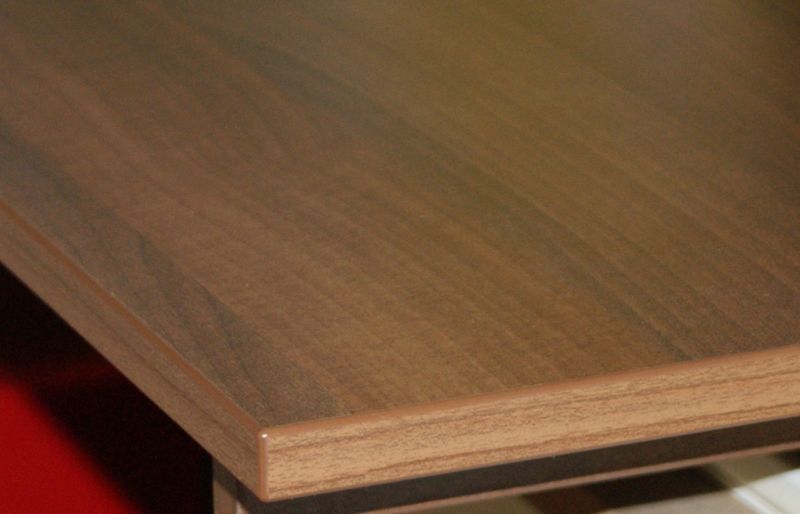
Melamine Faced Chipboard is the number one material for making fitted furniture and here we review its qualities and how it has progressed from a second-rate material to the material of choice.
Sometimes we get enquiries where the customer says they would like a material other than Melamine Faced Chipboard (MFC).
That’s fine as we have real wood veneered MDF, Birch Ply and primed MDF as other options.
However in many cases MFC is the ‘best’ choice because:
- it’s available in hundreds of different wood grain effects and colours
- it has an attractive hard-wearing surface that doesn’t not require varnishing/painting etc
- it’s cost effective and sustainable
Invariably the aversion to MFC is because the customer has had a bad experience with MFC furniture/kitchens in the past.
These experiences are well grounded but all the issues have been solved many years ago for those manufacturers - like us - who have chosen to use the solutions.
Here’s a run through of the issues and how they have been solved at the quality end of the market.
Myth 1 - The laminate chips and starts to peel away
First of all you need to start with a high quality manufacturer such as Egger or Kronospan. The surface quality of these products is excellent with some of the wood grain effects being almost indistinguishable from real wood. The laminate is thicker and well bonded. The weaker area for any MFC board are the edges. The solution to prevent chipping is to edge band the edges with 2mm thick ABS plastic. The norm for the kitchen industry has been to use 0.4mm thick melamine edging and the move is now towards 1mm thick edging. However quality manufacturers have been using 2mm thick edging for years. 2mm thick edging is very difficult to damage. Because it is ABS plastic it can take knocks and has sufficient give to avoid damage.
White MFC showing edged and unedged Walnut effect MFC with 2mm edgebanding
Myth 2 - Screws and hinges start to fall out
MFC doesn’t hold screws as well as solid Oak for example. The solution is to use the latest high-tech screws for joining the carcass and to use hinge fittings without screws. Screws hold in wood based products by cutting a thread. In solid wood the wood fibres are held tightly together, particularly in hardwoods like Oak. In MFC and MDF inter-wood fibre strength does not exist so we’re relying on the binders that hold the particles together. For short screws in particular any stresses on the screw (opening and closing a door for example) could eventually lead to it ripping out.The solution is rather than relying on cutting a thread in MFC instead rely on its resistance to compression forces.
For hinges we use Blum INSERTA which feature an expanding boss that activates when the flap is closed. Blum Inserta hinge and pre-drilled holes Inserta hinge flap opened Inserta hinge flap closed For hinge plates to connect to the carcass we use Blum Expando which features a 5mm diameter split dowel. As the fixing screw is driven in the split dowel expands.Hinge plates with expando split dowels
Because these pieces of hardware rely on compression they are much harder to pull out of MFC material.
Myth 3 - It warps and looks ugly
There was a time when the industry standard was 18mm thick for kitchens and 15mm thick for bedroom furniture. Quality manufacturers always use 18mm and avoid long material spans that could sag. An 18mm thick back panel keeps the carcass square and rigid. Modern board manufacturing techniques have increased the finesse of the finished MFC.
Egger for example produce boards in over seven different textures from ‘matt’ to ‘gloss’. The proof of course is in the results. See what our customers have produced.
Myth 4 - It’s made of rubbish
Cheaper MFC could have bits of debris - screws etc - in it but the MFC we use only has quality graded chips and binder. The reason being that when we process with automated machinery, the saw blades and cutters can cost several hundred pounds each and we don’t want them damaged by cutting a foreign object within the MFC! You may have seen water damaged cheap MFC where it starts to swell and pieces break off e.g the bottom of cheap kitchens. Well not the MFC we use! As a test we’ve left offcuts of Egger MFC outside exposed to the elements for a couple of weeks. Some swelling was evident but the offcuts were still serviceable (by the way we don’t leave customer orders out in the rain but if you took delivery of an order and for some reason left it out in the rain for several hours it wouldn’t be a problem).
Sustainability
MFC is one of the most sustainable wood based products. The bulk of the wood chips in MFC come from trees grown in managed forests. And because the trees are chipped there is very little wastage. Quality MFC is manufactured in the UK and is FSC certified. FSC stands for Forest Stewardship Council and guarantees that the product is made with wood only from sustainable sources. Just for comparison solid hardwood furniture on sale in the UK will almost certainly NOT be FSC (ask the retailer for the certificate!) and will have been manufactured in the far east. All of the MFC we use is FSC certified as are all the wood based products we use, down to an individual dowel.
Difficulties of making cabinetry with MFC - SOLVED
One reason why self-employed carpenters working alone in particular dislike MFC is that it is difficult to cut onsite. Without top grade tungsten carbide tipped (TCT) saw blades it is hard to avoid chipping the laminate. And then when the edge is cut, if it visible in the final installation then that edge needs to be have edge banding applied. Very hard to get good results that will last.That’s where the Fortschritt Bespoke Cabinetry service comes in. We do all the cutting and edge banding of custom sized parts in workshops using start of the art commercial grade machinery and deliver the parts to you ready for installation.
Here is an example of the type of saw used - not the type of thing an individual buys but manufacturing perfection
See for yourself
We can send sample swatches for any material including melamine. If you would like a couple of swatches please browse the material list and then send us an email with the material codes you would like.